Wupeeeeee....got me stuff from 3ge, caused bit of a mental barrier waiting...I know I could have got on on with other jobs but could not get it into my head that I NEEDED the stuff I bought.
Made one of my first bones ....worst one as well, being bottom rear....was very tempted just to do it ladder style ie get rid of that diagonal, but no I persevered. Tube mitre is very good but it still requires you to 'fettle' quite a lot, as using the tube thickness in the app would render it way to thin at the edges to mig so I guess everyone else has found a "halfy halfe" remedy to satisfy the critical dimensions and yes mine distorted too when fully welded but a little "heat line treatment" (a neat trick I learned at the shipyards)
brought the tubes back in spec to the mm .....in effect it cancels out the initial weld contraction so a few pics
using the cnc'd wooden jig
more than a couple of mm out should be 206
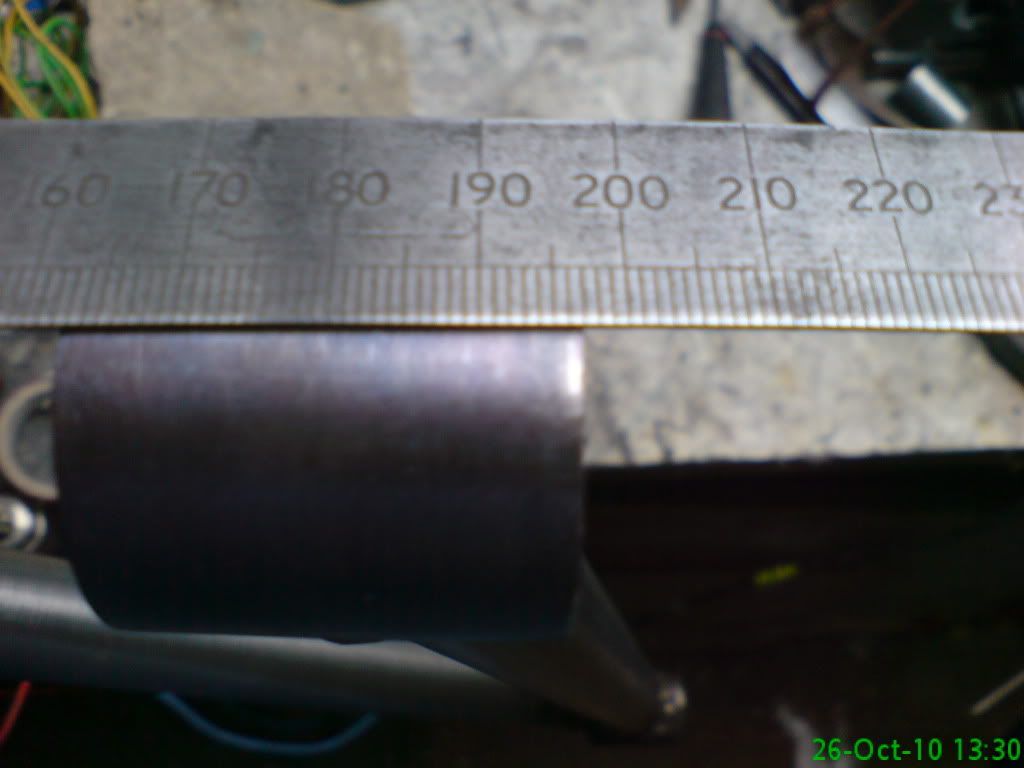
heat line treatment (has to be cooled immediatly with water but not dipped)
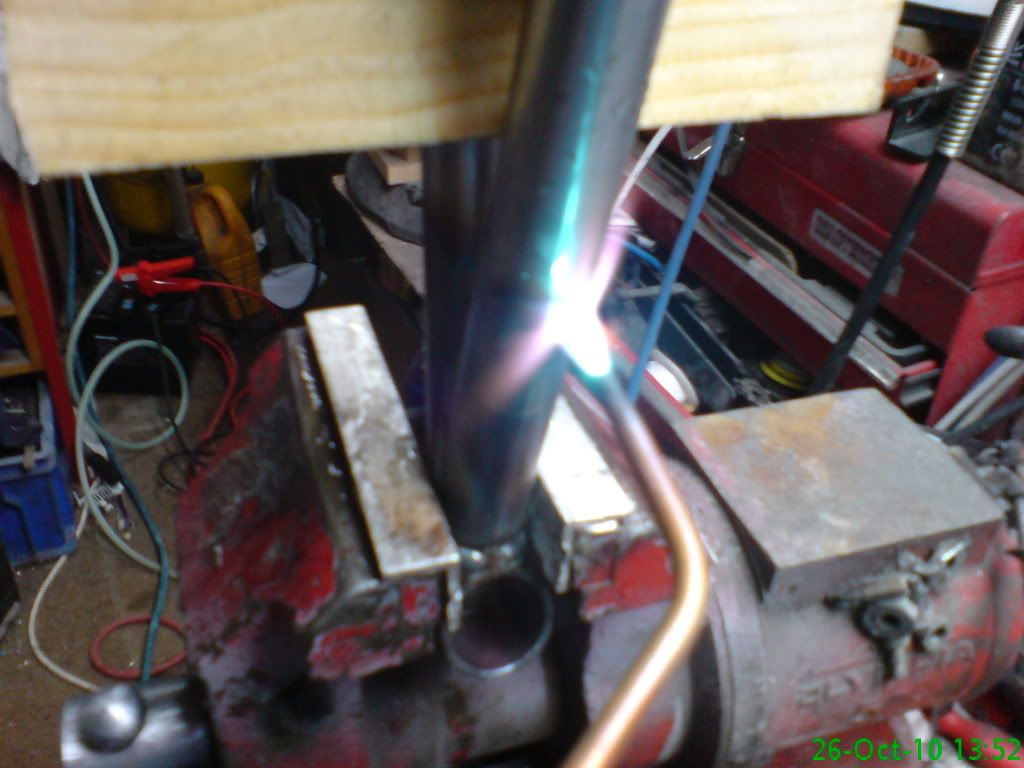
three of these treatments and a couple of strategically placed wedges and were right on the money no brute force used
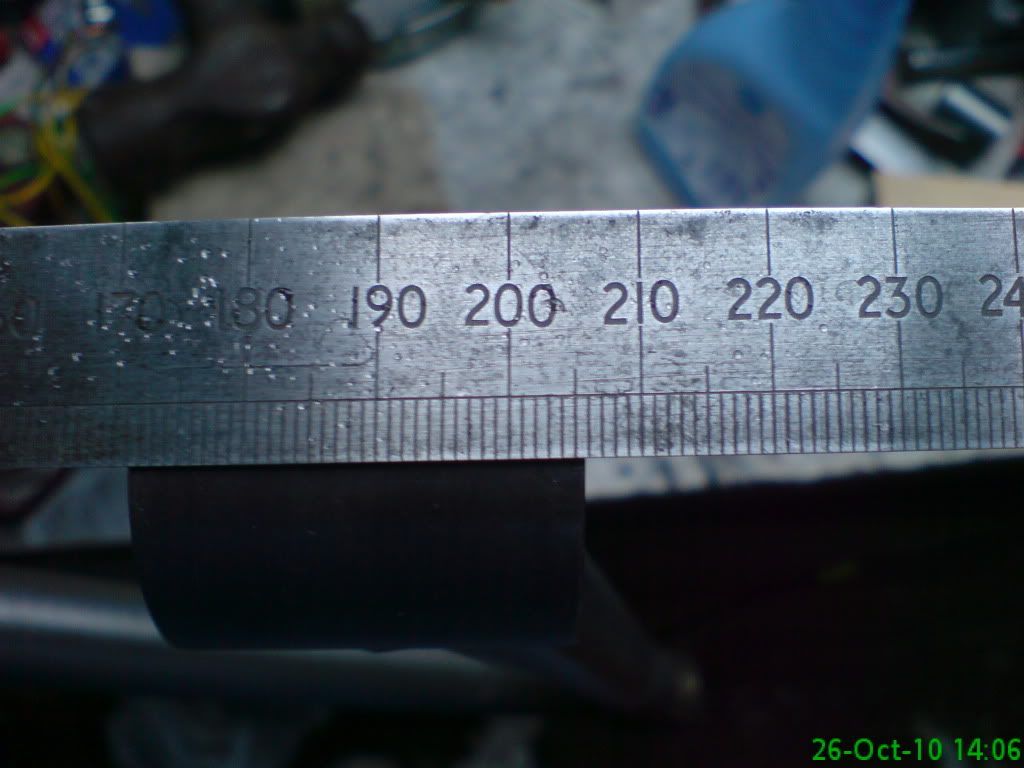
Next stage should be interesting as I intend to nickel plate the bushes and the 1st inch or so of tube for the ultimate in corrosion resistance.